|
|
|
Download e-Brochure |
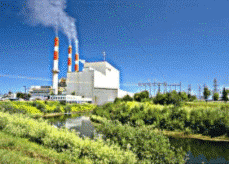 |
|
Customer SAVE
REAL Services' technically sophisticated clients included
establishments that are primarily engaged in the manufacturing of
Electrical
Power,
Transmission and Distribution of electrical power, and Specialty
Transformers and maintenance.
These electrical
generating stations maintenance plan
include Ferrography and
Oil Analysis; provided by REAL Services
along with our exclusive
SAVE REPORT that provides Return On Investment and Cost Justification
of your PM Program. |
|
Power Plant - Turbine Generator |
Case Study # 311 |
Gas Turbine Generator 1B
(297229); is one of three-(3) main turbines for GPP generation
facility. This unit was first rated
CRITICAL 9/25/2001.
Recommendation: Consider scheduling this equipment for
maintenance action in the near future. Specifically abnormal Aluminum
bearing wear. Compare past performance data with current information. |
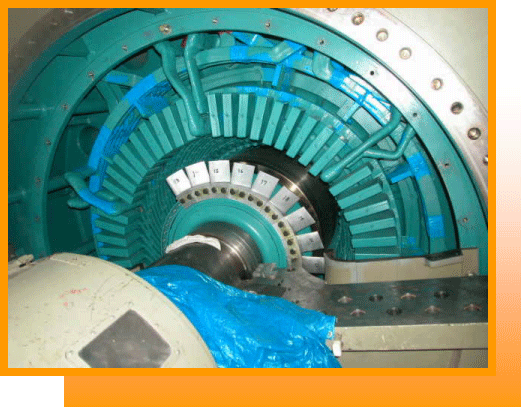 |
|
|
Although the equipment particle concentration (EPC)
had decreased for this equipment from 1,093 to 717 and is within
acceptable limits for this type of equipment, analytical results show
the presence of 70 micrometer (um) White Non-Ferrous Severe Sliding
wear and Cutting wear particles. Testing is also show the presence of
70um Rolling Contact (Bearing) wear particles. The Rolling contact
(Bearing) wear show the continued signs of tempering or rainbow
coloration from elevated temperatures at the critical contact point.
The Aluminum is the Babbitting from the Journal Bearing.
|
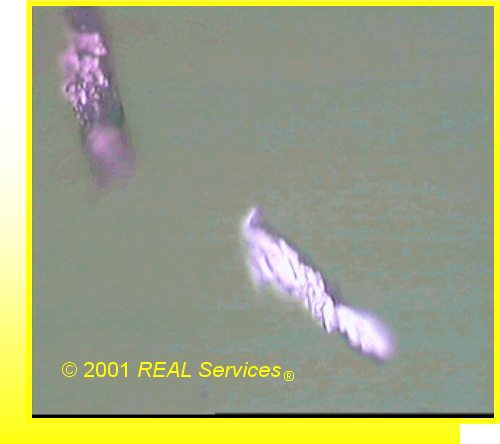 |
|
|
Upon opening of Gas Turbine Generator 1B (297229); the journal bearing
was found with significant striations with Varnish & Lacquer
accumulation as result of over heating of the oil. The sleeve is
composed of white non-ferrous metal that has been wiped.
Secondary Damage, Property Damage was minimized. Service Interruption
& Downtime was minimized. Maintenance scheduled and performed during
holiday weekend slow period.
Optimized equipment performance and savings for the utility, customers
and investors.
|
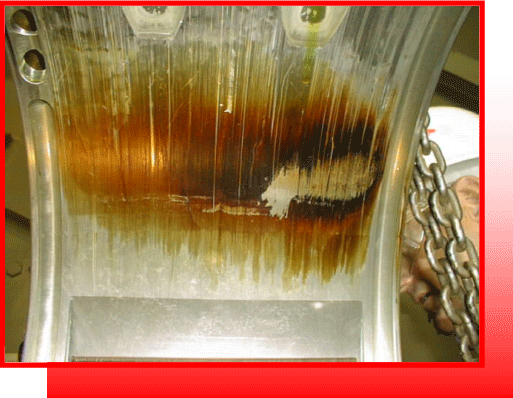 |
CUSTOMER ESTIMATED
COST SAVINGS: Original Component
Savings:
35,000,000
Secondary Damage Savings:
0
Down Time Min./Production hrs. Savings:
200,000
Business Interruption:
200,000
RUSH Shipping Cost Savings:
0
Parts & Inventory Warehouse Savings:
0
Overtime Repair Savings:
0
Total SAVINGS:
$ 35,400,000 |
|
|
 |
Making your PM Program mean ..... "Profit Making"ä
Experience Since 1985 |
800.483.R7E3A2L5 |
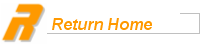 |
 |
© 2001-2012 REAL Services®
All Rights Reserved |